How to Properly Manage Textile Wastewater With Efficiency in MBBR
By: Tom Frankel
Post Date: May 16th 2019
Table Of Contents
- WASTE PRODUCED BY TEXTILE FACTORIES
- THE IMPORTANCE OF FINDING EFFICIENT WASTEWATER SOLUTIONS
- USE OF WATER IN TEXTILE INDUSTRIES
- TEXTILE INDUSTRY WASTEWATER CHARACTERISTICS
- TEXTILE WASTEWATER TREATMENT METHODS
- TEXTILE WASTEWATER TREATMENT PLANT DESIGN
- WASTEWATER SOLUTIONS FOR SMALL-SPACE TEXTILE FACTORIES
- AERATION SYSTEMS FOR FACTORIES WITH LIMITED SPACE
- BENEFITS OF AN MBBR IN THE TEXTILE INDUSTRY
Moving bed biofilm reactor (MBBR) is a relatively new and important type of wastewater treatment system. An MBBR tank consists of an aeration tank, very similar to a sludge tank, that contains unique geometrically shaped plastic material. This material provides extra surface area and encourages the growth of biofilm. The microorganisms that grow then consume the organic matter within the wastewater.
MBBR tanks allow for a higher concentration of biomass, which leads to space savings for any wastewater treatment plant. MBBR is useful for wastewater treatment plants that wish to increase their operating capacity and efficiency without increasing their building footprint. It is also helpful for wastewater treatment plants that continually experience high volume loads.
But why are MBBR systems useful for textile industry waste, and what advantages do they provide in this scenario? This article outlines a few textile waste facts and some reasons MBBR systems are ideal for textile wastewater. We will also provide ideas for how to manage these systems properly for the greatest efficiency.
Waste Produced by Textile Factories
Textile factories tend to produce a wide variety of waste products, including dyes, fats, oils and chemicals. During the rinsing process, in particular, it is nearly impossible to prevent some of these waste products from ending up in the water.
The Environmental Protection Agency (EPA) classifies hazardous wastes into three types:
- Nonspecific source wastes: These types of waste are specific materials that can come from several different types of industries. Many materials used in the manufacture of textiles are classed as nonspecific source wastes. For example, nonspecific source wastes include industrial chemicals such as solvents — like methylene chloride and toluene — resins, lye and even bleach. Chemicals such as white spirit — a reactive, colorless liquid made by distilling petroleum — are used in wool treatment and are termed nonspecific source wastes as well.
- Specific source wastes: These types of waste come from precisely pinpointed industries, such as petroleum refining or pesticide production. Textile manufacturing is not typically classed as one of these industries.
- Discarded commercial chemical products: These types of waste include off-specification products, container residuals and spill runoff or discarded spilled ingredients. In the textile industry, spilled chemicals such as solvents and bleach are discarded commercial chemical products.
Additionally, different types of textile manufacture processes produce different types of waste:
- Bleaching: The bleaching process typically produces waste chemicals such as hydrogen peroxide, sodium silicate and organic stabilizers.
- Scouring: The scouring process removes any organic impurities such as grease, fat, oil or dirt. Scouring typically produces waste products such as soda ash, sodium silicate and detergent, along with the organic material removed.
- Mercerising: This process, which involves treating cotton with caustic alkali to strengthen it and give it a shiny, silky look, typically produces waste chemicals such as alkali and sodium hydroxide.
- Equipment maintenance: The process of maintaining equipment typically produces a wide range of chemical waste. Waste products can include toluene, isopropyl alcohol, methylene chloride, different types of benzenes and different types of ethylenes.
- Carding, combing, spinning and machine lubrication: All these processes make use of oil for its friction-reducing effect. The oil then becomes a waste byproduct.
- Dying: The colored dyes used to make textiles bright and vibrant also become waste byproducts after use.
- Wool and synthetics finishing: These processes typically produce heavy metals such as chromium, copper, zinc and mercury.
These types of waste can be difficult and labor-intensive to remove from wastewater. But because of their harsh and toxic properties, many of them must be removed before wastewater can flow into municipal water systems.
The Importance of Finding Efficient Wastewater Solutions
Finding efficient wastewater solutions is critical for several reasons. The top three relate to cost, the environment and easing plant operations.
1. Cost
More efficient wastewater treatment processes lead to reduced costs overall. Greater efficiency leads to streamlined operations, quicker treatment and equipment that requires less repair and replacement. For example, a plant rendered inefficient because of high backflow in its equipment will find that it pays much more in energy costs. It may also find that it must significantly increase the number of repairs done on its blowers and likely replace them more frequently.
2. Environment
Environmental concerns also lead many plants to introduce as much efficiency into their operations as possible. If backflow or high headloss causes the motors to produce too much power, this results in higher financial costs as well as ecological costs to the environment. Similarly, if wastewater treatment makes ineffective use of heat recovery, the plant will use more heat and power than it should. This overuse comes at a steep cost in greenhouses gas emissions and resulting harm to the planet from textile industry pollution. Additionally, the outflow of waste that has not undergone thorough treatment can contaminate the surrounding soil and water. Textile industry pollution prevention is key to reducing this harm.
Heat recovery, in particular, is a critical step with which a wastewater treatment facility can dramatically heighten the energy efficiency of its operations. Heat recovery is a technique that applies process water, which has previously been used in the textile manufacturing process and is already warm, in place of electrical energy to heat cold freshwater. This step saves on expensive energy costs and helps keep greenhouse gas emissions low to reduce the effect of textile industries on the environment.
3. Ease of Plant Operation
Wastewater treatment is a complex process. The more efficiency plant managers can build into the process, the easier plant operation and maintenance will be.
Textile wastewater treatment involves many steps:
- Screening to remove small particles from the process water
- Oil removal
- Homogenization to distribute the pollutants evenly
- Neutralization to change the pH of the wastewater
- Chemical-physical treatment
- Biological purification such as aeration with MBBR
- Deinking to remove dyes
This multistep process can be time-consuming and requires many resources. It also requires precise calibration to be effective, and many issues can occur to impede the process. For example, if machinery or surfacing becomes clogged with sludge, this clogging has many unwanted effects that reduce the efficiency of the process. The more efficiency plants can build into their systems with durable equipment and cutting-edge methods, the more efficiently the wastewater treatment process will run, and the easier plant operators’ jobs will become.
Use of Water in Textile Industries
The textile industry is extremely water-intensive, consuming enormous amounts of water both for making the textiles and for treating the resulting wastewater.
Water is necessary at all steps of the textile production process. During the manufacturing process, textiles require water to wash the raw materials, and they also need water during the finishing process. Textile manufacture also uses water to flush the textiles of the pollutants used repeatedly throughout the production process, including dye, oil and chemicals.
Textile wastewater, including dye manufacturing, is a major environmental concern. The textile industry uses massive amounts of water — every kilogram of product requires about 100 to 200 liters, to be more exact. Legal requirements set by each country are stringent and reinforced heavily on wastewater. Efficient and reliable wastewater treatment processes must be available to meet these standards. Whether this is for the dye process or treatment, reduction in water use and an increase in reuse are the ultimate goals.
Water conservation has become a vital issue all over the globe. Wastewater treatment facilities must find ways to continue their efficient treatment processes while using less water. MBBR offers one way to do this.
Textile Industry Wastewater Characteristics
As discussed above, textile industry wastewater contains harsh pollutants, from dyes and resins to industrial solvents such as bleach and lye.
These waste products have a variety of undesirable or hazardous qualities:
- Oiliness: The oil used in as lubrication in textile manufacture gives an oleaginous quality to the resulting wastewater.
- Flammability: Oil is highly flammable, as are many other chemicals used in textile manufacture.
- Corrosivity: Several chemicals, such as bleach and lye, used in textile manufacture are incredibly corrosive. If they come into contact with vulnerable materials, they can do a large amount of damage.
- Reactivity: The sheer number of the chemicals involved in textile manufacture sets the stage for high reactivity when those chemicals come together in wastewater. Bleach and lye, for example, mix to form chlorine gas, a highly toxic substance.
- Toxicity: Many of the chemicals used in the textile industry, either in combination or singly, pose hazards to human health and the environment.
Just as these qualities require that these chemicals be stored carefully in the workplace, they also require the chemicals to be scrubbed thoroughly from textile wastewater. Proper treatment of textile industry effluents is necessary to ensure people and the environment remain safe from toxins.
Textile Wastewater Treatment Methods
One of the most tedious steps in the textile wastewater treatment process is the removal of dyes. Sludge, coagulation, adsorption and other removal processes are tedious, time-consuming and expensive. However, these methods can be useful in the absence of more cutting-edge techniques.
- Aeration: Aeration involves mixing oxygen into the wastewater column. Mixing in oxygen activates helpful bacteria, brings them into close contact with the biosolids in the wastewater, and allows the bacteria to break down the organic waste.
- Sludge: The activated sludge process treats wastewater by using a combination of aeration and an extra floc of bacteria designed to break down the organic components of wastewater. This process is effective but time-consuming — the food-to-microorganisms ratio must be carefully calibrated, and the sludge requires recycling at the end of the process.
- Coagulation: The process known as coagulation-flocculation involves adding polymers to the wastewater. These polymers collect small waste particles into larger clumps, and this coagulation of waste makes waste removal easier. However, though this process can remove a large percentage of organic waste matter, it cannot remove everything. This incomplete removal requires subsequent treatment methods.
- Adsorption: Adsorption takes place by binding liquid molecules to a solid. Typically, active carbon is introduced into the tank to bind the liquid molecules of wastewater. However, there are many types of light, highly water-soluble materials that adsorption cannot remove.
- MBBR:MBBR is a highly effective biological treatment process. An added benefit to the use of MBBR is it generally requires less space than activated sludge. This is due to the concentration of biomass. Furthermore, MBBR is suitable for high BOD or COD removal while having the advantages of both activated sludge and bio-film systems.
Textile Wastewater Treatment Plant Design
Usually, textile wastewater treatment plants that use MBBR systems contain a BOD/COD removal tank, from which water then flows to a separation tank. However, because of MBBR’s compact size and efficiency, plants often integrate it with other systems, such as activated sludge tanks or membrane bioreactors. The setup of these integrated systems becomes more complex.
Textile wastewater treatment plants should be designed with several factors in mind:
- Efficiency: The equipment and processes used in textile wastewater treatment plants should be as efficient as possible to reduce costs and limit the environmental impact of the plant.
- Types of contaminants: The design of a wastewater treatment plant should be optimized for the contaminants that will be present in the wastewater. If a large concentration of biosolids will be present in the wastewater, a treatment process designed to handle a high volume of biomatter will be necessary.
- Human impact: Textile wastewater treatment plants should also consider the human impact of their design and layout. For example, a treatment plant that contains untreated waste near the entrance of the facility may give off an unpleasant smell that neighbors dislike. Textile wastewater treatment plans should also dispose of their waste correctly so they do not contaminate the soil or drinking water. Proper waste disposal methods in the textile industry help keep the neighboring population safe.
- Space: Textile wastewater treatment plants should keep their space needs in mind. Without MBBR systems, a plant might need to accommodate several large treatment tanks to handle the volume of wastewater and its concentrated composition.
- Operational issues: Certain issues, such as feed pipe or effluent sieve blocking, nonhomogenous mixing, carrier blocking, carrier destruction and carrier overflow can sometimes occur with MBBR systems. Proper, skilled plant design can eliminate many of these issues.
Wastewater Solutions for Small-Space Textile Factories
For textile factories where space is limited, a few solutions exist:
- Aerobic treatment units: Aerobic treatment units (ATUs) are small and can fit into tight spaces. These types of units rely on mechanical aerator oxygen diffuser systems powered by blowers to deliver oxygen into the wastewater column, where aerobic breakdown can take place.
- Media filters and fixed activated sludge units: These types of solutions generally work well for treatment facilities with smaller flow rates, typically those seeing 1,000 to 5,000 gallons per day. Plants use media filters to reduce the number of suspended solids in wastewater, reducing the necessary sludge tank size. And activated sludge units have a low land requirement because they can handle a high volume of concentrated waste matter.
- MBBR: Because MBBR systems can handle a high concentration of biosolids, the treatment tanks used do not have to be large to be efficient and treat a high-volume flow. This factor makes them an excellent option for small-space textile factories.
Aeration Systems for Factories With Limited Space
Where space is limited, the choice of an aeration system should take the facility’s size constraints into account. Diffused aeration is often a wise choice because of the higher efficiency it provides over mechanical aeration.
- Coarse bubble aeration: Coarse bubble aeration has been shown to increase oxygen transfer efficiency by up to 150% when applied to an MBBR system, particularly one with a lower filling degree. The large bubbles cut incisively through the carrier bed to increase oxygen transfer efficiency (OTE).
- Rubber diffuser aeration: Diffused aeration using rubber diffusers is ideal for textile wastewater. Rubber diffusers are optimal for wastewater with a high concentration of biosolids because they will not cause backpressure or reduced OTE.
Benefits of an MBBR in the Textile Industry
MBBR systems offer many distinct advantages to textile industries.
- Space savings: MBBR systems are great space-saving systems. Their high organic load and hydraulic capacity mean they can do the same work as other types of aeration systems but within a smaller amount of space. Therefore, MBBR systems are excellent choices for textile factories with space constraints.
- Resistance to toxicity: The high concentration of biomass also means that an MBBR system is sturdy and can easily resist environmental alterations. For example, an MBBR system will not be adversely affected by the introduction of toxic chemicals that could otherwise cause toxic shock within the wastewater system. This factor makes MBBR an excellent choice for textile wastewater.
- Ability to treat strong waste: Because of the high concentration of suspended solids in an MBBR system, the system can handle very strong and concentrated types of wastewater, such as chemical wastewater. This factor makes MBBR systems ideal for textile wastewater.
- Improved nitrification: Nitrifiers grow slowly in comparison to other types of microbes, but the textured plastic carriers of an MBBR system provide a stable surface where they can grow safely and steadily. By supporting the growth of these nitrifiers, MBBR promotes improved nitrification within the wastewater and is ideal for wastewater with high nitrogen content.
- Efficiency: MBBR carriers are also continually bobbing in the wastewater because of the aeration system. Since they are always in motion, these carriers constantly bring their biofilm into contact with the wastewater. This factor leads to a high level of mass transfer and oxygen transfer efficiency to help speed up the wastewater treatment process.
- Easy maintenance: An MBBR system offers this specific advantage over traditional activated sludge systems, in particular. With traditional activated sludge, managing the sludge can be a laborious and difficult task. The balance of food versus microorganisms must be carefully calibrated to keep the system working effectively. With MBBR, no painstaking sludge calibration must take place.
- Cost savings: Managing activated sludge has many costs in time, money and resources. With traditional activated sludge systems, the sludge must be recycled, which also has high costs. With MBBR systems, no sludge recycling is necessary. This factor leads to lower costs. MBBR systems are also more cost-effective than membrane bioreactors.
- User-friendliness: MBBR systems are exceptionally user-friendly, especially for plant operators with no previous experience with MBBRs. Their low maintenance requirements make them easy to operate. Since microorganisms do much of the work, the plant operator has fewer controls to monitor and calibrate.
- Longevity: The biofilm carriers of an MBBR system are specially designed for a long life expectancy. This long life expectancy increases the longevity of the whole system.
Contact SSI Aeration, Your Full-Service MBBR Aeration Systems Provider
Coupling SSI’s patented PTFE fine bubble system with EEVolved MBBR allows plants to achieve the highest volumetric efficiency of any biological treatment process when compared to MBR, SBR, CAS and granular technologies. Our engineers have worked to reduce energy and operating costs, control complexity and operator intervention and decrease maintenance, all while increasing efficiency across all avenues of treatment, hydraulic capacity, volumetric efficiency, process versatility and process life span.
To find out more about how SSI can help in your textile treatment and MBBR needs, please contact us!
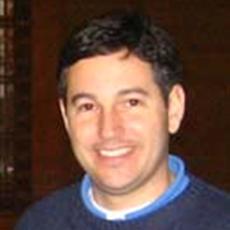
Mr. Frankel co-founded SSI in 1995 with experience in design and distribution of engineered systems. He is in charge of sales, marketing and operations in the company. Mr. Frankel holds multiple US patents related to diffusers. He is a graduate of Washington University in St. Louis.