MBBR Secrets from the Design and Manufacturing Side
By: Doreen Tresca
Post Date: August 5th 2020
4 to 20 g BOD/m2-day.
Once upon a time, someone published these values in a technical document as a guideline for MBBR design as a guide for achieving > 90% removal efficiency. These are the values that many designers live and die by. Where some are successful, others fail miserably. Applying a blanket approach to MBBR technology can lead to poor designs and poorer performance. Let’s level the playing field. What do these values really mean?
On a global basis, MBBR has become synonymous with plastic. More plastics extruders enter the market every year. Google MBBR and you’re likely to find photos of funny looking plastic cylinders with a price range starting at $100.00 USD/m3 to $1,000.00 USD/m3. Naturally, many buyers are questioning the range in prices. Don’t misunderstand me, extruders are a critical part of the supply chain, but this approach has taken the word “process” out of “MBBR Process Systems.” The best MBBR design teams understand this distinction. The focus has shifted away from Process and toward “where can I find the cheapest plastic.” End users and integrators need to be aware of this important distinction to make safe, informed decisions. For the sake of this discussion, let’s be honest. How much does your MBBR cost? If you’re going to buy cheap, then the answer is that you can multiply your initial investment by 3x. You should expect frequent replacement costs and high energy costs. That, I’m afraid to say, is the real long-term cost of your “MBBR.”
More about costs…
Resin costs fluctuate based on bulk volumes and location (as well as the stock market), but generally you will find the cost of raw material is roughly the same in the east vs the west for small production volumes. Larger production volumes and freight do impact cost, but the relationship reaches a plateau after only a few tons. In order to further reduce the cost of MBBR biofilm carriers, extruders consider two primary factors: 1) reduction in material or 2) use of questionable material properties. Just like many products in the world, someone came along and thought “I can make that cheaper.” (I generally prefer the phrase “more cost effective,” but in this case, cheap truly means cheap) The short answer is “Sure, you can find cheap production”, but as water and wastewater professionals, shouldn’t we be focused on the best long-term solutions where energy and product life are considered? If you aren’t, then you probably won’t be in business very long.
It follows that this reduction in material is directly correlated with structural integrity. If you were to collect samples of the various media being produced, you will find that some will crumble in your hands, while others can be hit with a cricket bat by Virat Kohli and survive. Reduction in material is often , but not always, correlated with reduction in specific gravity (Specific Gravity “SG” being the ratio of the density of material to pure water @ 4C in this case. SG should be an intrinsic property of the material used; however, reduction in biofilm carrier wall thickness is reduction in weight per piece, which will impact the density, buoyancy and mixing of a carrier. Density and SG are often used interchangeably, but they are technically different parameters). Density and SG are inversely correlated with energy consumption. In other words, the lower the density, the higher the operational energy consumption. Why is this true? If un-aerated water has a SG = ~1, and your media has a SG of 0.92, how much air is required to add to the liquid such that the SG ratio becomes even? QED: a lot. Designers often overlook the impact on water density as a function of temperature, process source and salinity. Salinity isn’t always a huge factor, consider Textiles with high TDS. A difference of 1 or 2% is possible.
We also hear of the word “weight” thrown around in the MBBR community. This is really reference to bulk density in most cases. In other words, how much does one 1m3 bag of media weigh? One media may have a bulk density of 95 kgs/m3, while the next may weigh 150 kgs/m3. There are variances in media geometries that account for some of this differential which is primarily related to the packing efficiency of the product. The real focus should remain on the impact of specific gravity. We discussed low SG, but what about high SG? Higher specific gravity arguably requires less operational energy to mix, but there is a point of no return. And I literally mean your media wont return…from the basin floor. Even approaching a 1:1 SG ratio is risky. Anything in excess of 1 SG and you’ve suddenly turned your MBBR into dead weight in an aerobic reactor. If you’d like your MBBR to last 1 to 2 years, then you can stop reading and continue on your quest for cheap plastic; however, if you’re interested in a process that will provide 20+ years of effective operation, a process than can be expanded in-situ, or a process that can increase your biological treatment capacity by as much as 500%, then you may be interested in reading more.
HDPE has been universally accepted as the best, long term MBBR material. This is true from both an operational perspective, but also as a manufacturing perspective. Operationally, HDPE is strong and has ideal material properties for energy efficiency mixing. In fact, modern HDPE biofilm carriers have been formulated for use with Fine Bubble Aeration. From a manufacturing perspective, HDPE is pliable, cost effective, generally readily available and is easily extruded. Turning back to the material properties, HDPE generally requires little to no modifications to make suitable for MBBR operation. Polypropylene, Polystyrene, Polyurethane, Polyvinyl Chloride, Polyvinyl Alcohol and others all have raw material properties that require additives to make suitable for proper MBBR operation. So, now that we’ve established HDPE is the most ideal material, what does it mean to have “virgin” HDPE. Many designers view “virgin” HDPE as the best specification for carrier material. Generally, I agree; however, virgin can still mean reprocessed material. Virgin can also mean FDA food-grade quality material which allows specific gravity up to 1.0.
Back to the 4 to 20…
We’ve established that material properties, media geometry and media design are only a few parts of the total MBBR equation. Any respectable MBBR process designer understands how to apply this technology into wastewater, but this can be where the “extruder” model comes up short. As an example, let’s think about the following: Project “A” is a textile. It has an average COD concentration of 800 ppm with a temperature of 30 °C and average flow rate of 1,000 m3/day. Project “B” is a Beverage manufacturer with COD of 800 ppm, a temperature of 30 °C and average flow rate of 1,000 m3/day. So, what Surface Area Loading Rate (SALR) do you choose? The short answer is that these applications require a completely different MBBR design and very likely different biofilm carriers. One application is readily biodegradable, while the other includes complex, long chain hydrocarbons that are difficult to break down. COD does not always equal COD. In other words, COD is not a universal design parameter. To say “I have a COD value of 800” does not give a complete picture. Apply 20 g BOD/m2-day to a textile application and you’re likely to end up with only 50% removal efficiency. Applying a blanket SALR for BOD (or COD) reduction across all wastewater application is perhaps the single biggest mistake designers make. I hear many people say “Well I used 20 g BOD/m2 for the last application and it worked well.” Great! But it does not automatically mean it will work for the next application.
What then, is the best method for MBBR designs? This is a question I get asked on a weekly basis. The world has created a need for innovation and cost-effective treatment methods. In many cases, it has unfortunately led to improper application of many technologies in our efforts to find competitive advantages. In our design group, many times we are simply given: 1) a flow rate, 2) inlet BOD (or COD) value, and 3) the effluent BOD (or COD) objective. While we can make general assumptions and provide a seemingly endless list of exceptions, this is not the ideal way to proceed. A correct problem definition is the first step. An understanding of the type of wastewater is the next step. Again, COD is not universal. The COD value to be treated in Textile vs the COD value to be treated in Beverage production are completely different types of COD. While it is true that MBBR designs revolve primarily around SALR values, it is not the one and only method. And while it is also generally true that the SALR relationship follows a positive relationship with temperature, it is not always true. Figure #1 below shows the general relationship of Temperature vs SALR.
Figure #1 can become twisted and distorted. It is not universal and cannot be applied to all MBBR designs. The following are a list of factors that will shift the SALR curve in one direction or another:
- Soluble BOD vs Particulate BOD
o Bacteria will primarily focus on soluble BOD. The more sBOD, then generally the better the outcome.
- COD:BOD ratio
o This is used as a rule of thumb to gauge the biodegradability of wastewater. Soluble fractions should be normally be considered for design purposes.
- TSS:BOD or TSS:COD ratio
o This is also a gauge for the composition of the wastewater. Lower TSS and higher BOD may mean more soluble is present.
- Nature of the process water
o Is the wastewater of organic or synthetic source? What is the relationship of Carbon (C) and Hydrogen (H) bonds. Presence of longer chain hydrocarbons, phenols, etc impact how biofilm responds.
- TDS
o Impacts osmotic pressure, saturation and oxygen transfer.
- % open area of biofilm carrier
o Higher Surface Area biofilm carriers often have lower % open area. Applying excessive SALR to these types of carriers will lead to loss of “diffusion-able” surface area and decrease in performance. This has been noted for chip, foam and gel biofilm carriers following long term operation.
- Surface area of biofilm carrier
o As noted above, generally it follows that the higher the specific surface area, the lower the SALR rate should be applied to avoid diffusion limitations. Many studies have shown that the aerobic diffusion boundary is on the order of a few hundred microns (< 500 um). In other words, having “more” or “thicker” biofilm attachment does not necessarily mean better aerobic BOD/COD performance.
- Presence of inorganics and chemicals
o Excessive inorganic material or chemical may eventually take up valuable surface area on the biofilm carriers and reduce area for actual biofilm growth. Operation in the first years may not be impacted, but the longer term implications are dire.
- Mixing energy
o This is a bit of a chicken and egg equation, but higher SALRs generally require more mixing to ensure effective, long term diffusion and scour.
o As briefly mentioned above, energy is inversely related to SG. Take your 5,500 m2/m3 “chip” style media at 0.92 SG and you’ll find it requires up to 3x the energy density to uniformly mix. You may be surprised that the cost of your MBBR after year #1 is 3x greater than you expected.
In the end, the reality of the MBBR design is that you end up with a chart more closely resembling that of Figure #2 below with a multitude of design curves for different applications and for different factors.
Of course this is still just a glimpse into what accurate and effective MBBR designs require. As MBBR is part of an overall treatment solution, understanding how MBBR integrates into the total flow sheet is critical. Studies have shown that aeration intensity and Retention Time have a direct impact on the effluent solids of a biofilm based system. The higher the aeration intensity, the higher the likelihood that your effluent TSS will be elevated and will likely be difficult to settle. Type of aeration also plays a factor in suspended solid levels and settling properties. Understanding how MBBR integrates into solids separation is also a critical part of the overall design. As MBBR will convert soluble into biological solids, these solids also have to be effectively removed to meet effluent objectives.
MBBR has been developed for nearly 30-years and yet continues to evolve. Most engineers and process experts view biofilm technology as the future of wastewater treatment due to it’s ability to produce higher efficiency in smaller footprints compared to traditional approaches. The versatility of MBBR continues to be explored with newer treatment applications each year. From municipal to textiles, MBBR is a proven process technology.
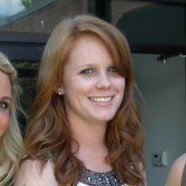
Mrs. Tresca is in charge of SSI’s Marketing Department. In addition, she is involved in sales and and believes in putting “customers first.” Mrs. Tresca is a graduate of the University of Buffalo.