What Is the Best Wastewater Treatment System for Textile Plants?
By: Tom Frankel
Post Date: June 14th 2022
It’s important for textile factories to have an effective wastewater effluent treatment plan. Textile production processes are water-intensive and release harmful chemicals, dyes, acids and starches into the water. Textile effluent can cause significant water pollution that threatens human health and damages the environment.
The textile industry uses many industrial processes and substances that require physio-chemical treatment of the water used in those processes. Since textile wastewater is so harmful, textile plants must have an appropriate effluent treatment system to treat water effectively while saving time, space and money.
The most effective wastewater treatment method is the moving bed biofilm reactor (MBBR) method. The MBBR method is the best wastewater treatment for the textile industry because it’s efficient, cost-effective, long-lasting and beneficial to the environment. Learn more about textile wastewater and the MBBR method of wastewater treatment.
Table Of Contents
- Textile Wastewater Characteristics
- Processes That Produce Textile Wastewater
- Types of Textile Wastewater Treatment
- Best Membranes for Textile Wastewater
- Increasing the Efficiency of Textile Wastewater Treatment
- Learn More About Our Textile Wastewater Treatment Options
Textile Wastewater Characteristics
Textile industries use various chemicals, dyes, acids and starches that produce harmful wastewater. Textile wastewater has the following hazardous characteristics:
- Toxicity: Chemicals used in textile processes are highly hazardous to the environment and human health.
- Corrosivity: Many chemicals used in manufacturing textiles are corrosive. Chemicals such as lye and bleach can damage vulnerable materials.
- Oiliness: Oil is used as lubrication in textile processes, resulting in oily wastewater.
- Reactivity: Certain chemicals can react with one another and create hazardous substances. The textile industry releases many chemicals that can react when they combine in wastewater.
- Flammability: Many substances used in textile production are highly flammable.
Textile wastewater pollution poses a serious threat to environmental and human health. To keep the environment and our water systems safe, textile wastewater treatment removes the following contaminants from water:
Chemicals
Many chemicals are used in the textile industry. Chemicals help to create the following textile finishes:
- Anti-microbial finish
- Fire-resistant finish
- Crease-resistant finish
- Anti-static finish
- Easy-care finish
- Hydrophilic finish
- Non-slip finish
Since chemicals are needed to create these fabric finishes, the chemicals also enter textile wastewater and must be removed to protect the environment. Different finishing processes include the following chemicals:
- Formaldehyde
- Silicone
- Phenols
- Organo-silver
- Quaternary ammonium compounds
- Oxy-ethylated polyamides
- Silica gel
- Chlorinated flame retardants
- Brominated flame retardants
- Phosphorous-containing flame retardants
- Poly ammonium quaternary salts
Dyes
Textile dyeing also poses a need for wastewater treatment. Synthetic dyes are non-biodegradable and toxic, posing a significant threat to the environment. They are present in textile wastewater and seriously affect human health, soil fertility and crop production. The textile industry uses the following dyes:
- Anthraquinone dyes
- Azo dyes
- Xanthene dyes
- Indigo dyes
- Phthalocyanine dyes
- Diphenylmethane and triphenylmethane dyes
- Nitrosated and nitrated dyes
- Polymethinic dyes
- Cationic or basic dyes
- Reactive dyes
- Metalliferous dyes
- Substantive or direct dyes
- Sulfur dyes
- Dispersible dyes
- Vat dyes
- Pigments
Textile dyeing processes release undesirable dye effluents into wastewater. If wastewater is left untreated, these dyes can pose significant threats to aquatic environments such as oceans, rivers and lakes.
Since they lack biodegradability, they can damage aquatic environments’ essential conditions. Dyes also prevent light penetration to aquatic environment depths, which reduces photosynthesis to aquatic flora and changes the nature of these environments.
Starch
Starch has been used in the sizing and finishing processes of textile production for centuries. It is a finishing agent traditionally used to improve rayon and cotton fabrics’ appearances. It’s also used during the sizing process to give yarn properties that aid in weaving. It removes wrinkles that form during preparation and adds gloss to fabrics.
Starches used in the textile industry release high-strength organics that must be reused or removed from wastewater. The main starches used in textile production include the following:
- Potato
- Corn
- Sago
- Cassava
- Rice
- Wheat
Fabrics
Textiles and fabrics contain fibers that can produce contaminated wastewater. Textile plants can create many different fabrics, including the following:
- Denim
- Velvet
- Felt
- Mohair
- Fleece
- Muslin
- Brocade
- Gabardine
- Gauze
- Poplin
- Crepe
- Flannel
- Tweed
- Demask
- Corduroy
- Chintz
- Gingham
- Chiffon
- Taffetta
- Terrycloth
- Fustian Fur
Acid
Textil production also produces wastewater with harmful acids. Some of the acids used in the textile industry include the following:
- Hydrochloric acid
- Sulfuric acid
- Phthalic acid
- Citric acid
- Formic acid
- Acetic acid
- Nitric acid
- Liquid ammonia
- Oxalic acid
Processes That Produce Textile Wastewater
Textile factory fiber production consists of wet and dry processes. The wet process uses safe, potable water and produces contaminated wastewater that must be treated before it is released. The wet process includes the following steps:
- Sizing: During the sizing process, starch, enzymes and waxes are applied to yarn to improve its strength so it can withstand strain and stress during weaving.
- Desizing: After the yarn is woven, the fabric is washed or desized. The products used in desizing depend on the chemicals used to size the yarn and can include enzymes, oxidizing agents, acids and surfactants.
- Scouring: Scouring is the process of cleaning fibers before dyeing them. It includes the use of soaps, surfactants, pectin, fats, sizes, oils, waxes and sodium hydroxide.
- Bleaching: This decolorization process removes coloring components from a raw textile material. This process produces wastewater containing stabilizers, alkaline conditions, sodium silicate and hydrogen peroxide.
- Mercerising: Mercerising treats fabric with various chemicals, such as sodium hydroxide, zinc chloride and sulfuric acid, to increase its strength and improve dye update.
- Dyeing: Dyeing adds color to fibers, and it produces contaminants such as surfactants, metals, color, salt, acids and alkali.
- Printing: The textile printing process releases contaminants such as formaldehyde, metals, solvents, urea and color.
- Finishing: The finishing process converts fabrics into usable materials, and it releases contaminants such as solvents, softeners, waxes and resins.
Types of Textile Wastewater Treatment
There are various ways to treat wastewater in textile plants, but some methods are more beneficial than others. Textile industry wastewater treatment processes include the following:
- Absorption: The absorption process binds liquid wastewater molecules to a solid such as active carbon. However, absorption cannot remove all contaminants. Some contaminants are too light and water-soluble for absorption to remove.
- Aeration: During the aeration process, oxygen is added to a wastewater column, which activates beneficial bacteria and allows them to break down organic waste.
- Activated sludge: The activated sludge wastewater treatment process combines aeration and additional bacteria, which break down organic components in the wastewater. This process is very time-consuming because the ratio of food to microorganisms must be accurately calibrated. Additionally, the sludge must be recycled at the end of the process.
- Coagulation-flocculation: The coagulation-flocculation process adds polymers to wastewater, which combine small contaminant particles into larger clumps. While this process is relatively easy, it requires additional wastewater treatment methods because it cannot remove all waste particles from the water.
- MBBR: MBBR is the most effective textile wastewater treatment. It uses biological processes to remove contaminants from wastewater.
MBBR
MBBR is a biological treatment method, meaning it includes biofilm technology and aeration processes. During this process, water enters an aeration tank containing media made of small, geometrically-shaped plastic chips. The media grow biofilm organisms that remove contaminants and waste from the water. The media move throughout the tank via an aeration grid so the biofilm organisms can efficiently consume contaminants.
This treatment method is beneficial for textile plants that treat continuous high-volume loads and plants that wish to save space. An MBBR tank saves space by allowing a higher biomass concentration, letting textile plants improve their wastewater treatment efficiency and operating capacity without increasing their building size.
Benefits of MBBR in Textile Plants
MBBR wastewater treatment is an important type of wastewater treatment because of its many benefits.
- Faster water treatment: The MBBR treatment method takes less time to treat water because you can place MBBR media in an existing tank, which allows you to treat water efficiently.
- Longer life span: PTFE membranes that hold bacteria in the MBBR system are durable and long-lasting, which gives the overall MBBR system a long life span.
- Reduced hydraulic retention time (HRT): HRT is the average time the substrate remains inside the digester. The MBBR method reduces the amount of time the wastewater has to sit in the tank until it moves on to the next treatment stage.
- Self-sufficiency: The MBBR method is very self-sufficient, so textile plant operators do not have to hire anyone to closely monitor the machinery or processes, saving time and money. With fewer controls than other systems, the MBBR system is easy to operate.
- Greater hydraulic capacity: MBBR systems can handle more water than alternative systems, making them more efficient.
- Space-saving qualities: The organic load rate (OLR) is the organic matter feed-in per unit time and volume of the reactor. A greater OLR allows the MBBR method to save space.
Best Membranes for Textile Wastewater
Common wastewater treatment membranes include EPDM membranes and PTFE membranes. EPDM membranes are made from rubber, while PTFE is made from synthetic polymers. PTFE membranes have the following qualities:
- Durability and density
- Self-lubrication
- Nonstick
- High density
- Low tensile strength
PTFE is useful in many industries, including the textile and medical industries, and for creating Teflon. Since it has nonstick properties, it helps prevent bacteria aggregation and infections in hospital settings. It’s also the best material for textile wastewater treatment. PTFE membranes emit small bubbles through holes in membrane surfaces to mix water, transfer oxygen and facilitate aeration. PTFE membranes have the following benefits:
- They last longer: PTFE membranes have a high density, so their surfaces are more resistant to penetration, breakdown and foiling. PTFE membranes also maintain their beneficial qualities over time. As PTFE membranes age, they are less likely to have a reduced bubbling area or develop plasticizer creep.
- They maintain durability: Due to their hydrophobic properties, PTFE membranes are less vulnerable to swelling and cracking than EPDM membranes are. They can remain stationary in water and maintain their durability. They can also withstand harsh chemicals.
- They require less cleaning and maintenance: Because PTFE is nonstick, it is difficult for organic matter to gather and cling to PTFE surfaces. This helps to reduce the rate of membrane fouling, and it requires less frequent cleaning than EPDM membranes.
PTFE membranes work well with the MBBR method because they require less maintenance and less airflow. They also reduce power consumption because they maintain durability even when the wastewater treatment system is turned off and remain stagnant in the water.
Increasing the Efficiency of Textile Wastewater Treatment
Efficient wastewater treatment is important for several reasons. It protects the environment, reduces costs and simplifies textile plant operation. Implementing a more efficient wastewater treatment method has the following benefits:
Environmental Efficiency
An efficient wastewater treatment method can prevent environmental damage in the following ways:
- Motor efficiency: Efficient wastewater treatment prevents high headloss and backflow, saving power.
- Effective heat recovery: Efficient wastewater treatment uses effective heat recovery, which prevents textile plants from using more power and heat than they should. This results in fewer greenhouse gas emissions.
- Pollution prevention: Efficient wastewater treatment prevents harmful substances from contaminating the environment.
Effective heat recovery makes wastewater treatment most efficient. The heat recovery process utilizes warm water that has been previously used in textile production. It eliminates the need for more energy to heat freshwater because it uses water that is already warm, reducing greenhouse gas emissions and water consumption, which is healthier for the environment.
Cost Efficiency
Efficient wastewater treatment reduces costs in the following ways:
- It streamlines operations for faster water treatment.
- Equipment requires fewer replacements and repairs.
- It reduces energy costs.
Operational Efficiency
Plant operation and maintenance are easier with an efficient wastewater treatment method. Textile wastewater treatment includes the following steps:
- Small particle removal from process water
- Oil removal
- Even particle distribution via homogenization
- Changing the wastewater pH through neutralization
- Chemical-physical treatment
- Purification
- Removing dyes through deinking
Efficient methods and durable equipment can reduce the time and resources required to complete the listed steps and treat wastewater in a textile plant. A wastewater treatment process is most effective with precise calibration and little to no impeding issues. Plant operators will find their jobs easier and spend less time on maintenance with an efficient wastewater treatment method.
Learn More About Our Textile Wastewater Treatment Options
Textile industry wastewater is hazardous to the environment and human health. Textile production releases harmful and toxic contaminants into the water, and they must be removed to prevent wastewater pollution. While many wastewater treatment methods are available, the most effective wastewater treatment method for the textile industry is the MBBR method.
The MBBR method helps textile factories save money, reduce their power and water consumption, effectively remove contaminants from water and save time. When textile plants use PTFE membranes and the MBBR wastewater treatment method, they can decrease the amount of time, money, power and effort they spend on treating their water and instead spend their time on other essential tasks.
SSI Aeration offers efficient textile wastewater treatment plans and systems. With high-quality, reliable products and an expert engineering department, SSI delivers top-notch wastewater solutions for any industry. SSI’s highly efficient and long-lasting MBBR system produces unparalleled results to help textile factories effectively treat their water with little maintenance.
With SSI Aeration, textile plants can expect the safest and most effective wastewater treatment process. Contact SSI Aeration to learn more about our textile wastewater treatment options.
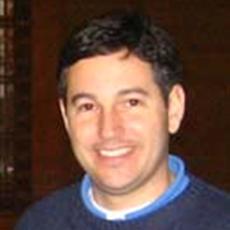
Mr. Frankel co-founded SSI in 1995 with experience in design and distribution of engineered systems. He is in charge of sales, marketing and operations in the company. Mr. Frankel holds multiple US patents related to diffusers. He is a graduate of Washington University in St. Louis.