How to Reduce Wastewater Treatment Operating Costs
By: Tom Frankel
Post Date: marzo 23rd 2023
Wastewater and sewage treatment plants are essential to industries and municipalities across the U.S. They ensure wastewater is safe for return to waterways or reuse in other commercial processes. Wastewater treatment plants are crucial for preserving the environment and protecting human health. However, the cost of wastewater treatment operations can be high.
Wastewater treatment requires high energy consumption, the use of chemicals and other materials, waste disposal and a skilled and well-trained workforce. With shrinking budgets to cover the necessities, many wastewater plants are looking for ways to reduce operational costs.
What Is the Average Cost to Run a Wastewater Treatment Plant?
The average cost to run a wastewater treatment plant depends on several factors, including:
- How much water flows through the plant daily.
- The plant’s sludge removal system.
- Which industry produced the wastewater.
However, there are four main operational costs that every wastewater treatment facility will incur — workforce, waste disposal, energy consumption and materials. Each of these operating costs is necessary for running a treatment plant.
1. Workforce Costs
One of the highest costs for a wastewater plant is its workforce. Many wastewater facilities operate for extended periods — some even work non-stop throughout the year. As a result, many treatment plants require staff on call 24 hours a day to ensure the facility runs smoothly. The plant’s size and automation level are two significant factors influencing workforce costs.
Because staff members are responsible for everything from leaking pipes to industrial and electrical equipment, they must also be trained and certified to work in wastewater treatment plants.
2. Waste Disposal Costs
Waste disposal is another significant cost when running a wastewater treatment plant. Plants must be able to dispose of waste like sand, screenings and various types of sludge. Disposal costs vary depending on:
- Local and national regulations on the disposal of organic ad inorganic waste.
- Local waste disposal prices.
- Disposal method.
3. Energy Costs
Many treatment plants run for extended periods and require significant power to run various equipment. As a result, energy is one of the highest operational costs for wastewater treatment plants. While the primary and secondary stages of water treatment typically use the most, nearly every process requires energy, including:
- Aeration tanks and aeration sand traps.
- Pumping stations.
- Digestion facilities.
- Sludge screening.
- Preliminary and secondary sedimentation tanks.
4. Materials Costs
Wastewater treatment plants use chemicals and other materials to clean and stabilize wastewater. They often use high quantities to achieve the required level of cleanliness, making materials one of the main operational costs for any treatment plant.
The cost of chemicals and other materials will vary by the type and quantity the plant uses, which will depend on the type of wastewater and how clean it needs to be. Global, local and national pricing structures and supply levels may also impact the cost of chemicals.
How To Reduce the Operational Cost of a Wastewater Treatment Plant
The rising costs of electrical energy and chemicals essential to wastewater treatment are forcing many plants to find ways to manage expenses. There are various ways to reduce the average operational cost of a wastewater treatment plant, from upgrading equipment to automating operations. While some of these methods may require an initial upfront investment, they can provide considerable long-term cost reduction.
Here are 10 ways to reduce operational costs:
1. Upgrade Pump Stations
Modern pumps, motors and drives are more efficient than older pumps. Older pumps usually work at one speed with an on-off cycle. Modern pumps and variable frequency drives can adjust pump speeds to flow rates, helping reduce energy consumption in the long run.
2. Optimize Aeration
Plants can use the following methods to optimize their aeration:
- Consider upgrading aging equipment such as blowers, diffusing systems and air distribution components to newer, more efficient models.
- Use variable frequency drives to make older blowers more efficient instead of relying on adjusting the inlet valve to match demand.
- Reconfigure the aeration basin by switching to fine or ultra fine-pore aeration systems that increase oxygen transfer efficiency while reducing power usage.
- Ensure existing aeration systems are well-maintained.
3. Improve Sludge Management
Improving sludge management in the primary treatment stages can considerably impact processes and equipment downstream. Grit in sludge can damage equipment downstream, build up in areas where flow is slow and increase wear and tear on equipment. Removing as much grit as possible in early treatment can improve the equipment’s life span and reduce the risk of sudden failure. Biogas from sludge can also produce electricity or heat water, reducing energy consumption.
4. Recover or Recycle Essential Nutrients
Look into the feasibility of recovering and recycling phosphorous. Wastewater plants can recycle phosphorous into commercial-grade fertilizer, providing an alternative revenue stream. Removing these nutrients can also improve sidestream performance by lowering the nutrient load in recycling streams.
5. Reduce Chemical Disinfection
Ultraviolet (UV) light disinfection is becoming more commonplace in wastewater treatment. UV systems provide a high level of disinfection and reduce the need for expensive and hazardous chemicals like chlorine. Treatment plants using UV disinfection systems can reduce chemical costs and create a safer working environment.
6. Update Lighting and HVAC Systems
Lighting, heating and cooling require considerable energy. Update lighting and HVAC systems to newer, more efficient models for energy savings. Rebates may also be available for certain improvements.
7. Leverage Gravity
Where possible, leverage gravitational forces. Look for areas where gravity can move water rather than relying on electric motors.
8. Automate Operations
Automate as many processes as possible. Automated processes require less human intervention and provide in-depth data on a treatment plant’s operations. The data from automated systems can help plants:
- Optimize operations.
- Reduce energy consumption.
- Reduce chemical consumption.
- Reduce workforce costs.
9. Adjust the Size of Installed Equipment
Some equipment may be too large or too small for the flow a plant receives. Replacing oversized equipment with smaller, more efficient equipment can cut costs. In other areas, replacing several smaller lower units with one larger, more efficient unit can significantly lower energy consumption.
10. Diagnose Costly Processes
Before taking steps to reduce costs, wastewater treatment plants must identify and diagnose their most costly operations. Knowing which systems, processes and equipment cost the most will help determine the next steps.
Here are a few steps to properly diagnose and address costly processes:
- Perform a pilot study to gather operational efficiency and costs information.
- Use data analytics to analyze and interpret pilot study findings.
- Benchmark current costs and energy usage throughout the plant.
- Undertake a forensic analysis to understand the life span of different equipment.
- Leverage artificial intelligence to test potential changes and identify areas for optimization.
- Train staff to improve workflows and efficiency.
- Perform maintenance where required.
- Upgrade or replace systems and equipment.
Contact SSI Aeration, Inc. for Cost-Reducing Solutions
Cost reduction is becoming increasingly crucial for all industries. SSI Aeration, Inc. has a team of experienced engineers who work with wastewater treatment plants to optimize processes and reduce costs. Take advantage of SSI’s wide range of industry-leading wastewater treatment products to make treatment more effective and efficient.
Contact SSI Aeration, Inc. today for effective cost-cutting solutions.
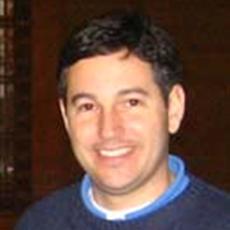
Mr. Frankel co-founded SSI in 1995 with experience in design and distribution of engineered systems. He is in charge of sales, marketing and operations in the company. Mr. Frankel holds multiple US patents related to diffusers. He is a graduate of Washington University in St. Louis.