What Is the Best Process for Treating Wastewater in Every Industry?
By: Tom Frankel
Post Date: Giugno 29th 2023
What Is the Best Process for Treating Wastewater in Every Industry?
Facilities like food and beverage and chemical and textile manufacturing rely on water for their operations. Whether iron and clay particles from mining operations or dyes and acids from clothing production, harmful contaminants can quickly find their way into industrial water. This makes wastewater treatment a pivotal process across many industries.
Wastewater treatment removes as much of the suspended solids as possible before discharging the water back into the environment. This process prevents contamination of waterways to protect both humans and the environment. Read on to learn about different types of wastewater treatment and how various industries use them.
How Does a Wastewater Treatment Plant Work?
Wastewater treatment plants use physical, chemical and biological processes to treat and remove contaminants from industrial wastewater. Most facilities follow these stages of wastewater treatment.
1. Pretreatment
During this phase, wastewater flows into treatment tanks. Bar screens — large filters that remove solids from the wastewater — filter out debris like leaves, branches and plastic. Grit chambers filter out small particles like sand, gravel and dirt, while equalization (EQ) tanks help stabilize water flow to promote settling.
Some industrial wastewater treatment methods involve chemical pretreatment. Chemical treatment of wastewater alters the water’s pH or its contaminants’ structures. As a result, the solid waste particles stick together, creating heavier waste compositions that can precipitate out easier. These processes are called flocculation and coagulation.
2. Primary Treatment
In the primary treatment stage, the pretreated water moves into a primary clarifier. A primary clarifier is a device with a circular or rectangular tank allowing substances to settle or float, separating them from the wastewater.
The wastewater sits for a while, filtering out additional particles. If the plant doesn’t remove fats like grease and oil during pretreatment, it skims them during primary treatment.
3. Secondary Treatment
During secondary sewage treatment, microorganisms break down more solid matter in the wastewater. There are different types of secondary wastewater treatment, such as:
- Anoxic: Anoxic treatment converts nitrate (NO3) nitrogen into molecular nitrogen gas. It occurs in the absence of free molecular oxygen.
- Anaerobic: Anaerobic treatment takes place in the absence of all oxygen forms. Typically, it involves covered digestion lagoons that help the anaerobic bacteria break down organic waste.
- Aerobic: Aerobic treatment takes place in the presence of oxygen, so the facility must have oxygen-supplying equipment to aerate the wastewater. They can use lagoons with surface aerators or aeration disc diffusers.
4. Tertiary Treatment
Tertiary treatment of wastewater offers additional filtration and disinfection. This stage is usually optional. Facilities often use it when they have rigorous wastewater requirements to meet. Tertiary treatment might involve processes like chlorination, ultraviolet disinfection, ozone treatment and ion exchange.
Once the water meets the necessary regulatory guidelines, the plant can discharge it back into the environment. The treated wastewater — or effluent — mixes with the existing groundwater or surface water. It can then be reused for industrial processes or sent for treatment and used as drinking water.
Wastewater Treatment Processes for Different Industries
Wastewater treatment can look slightly different for each industry, as manufacturing processes vary in the types of contaminants they face. Here are some industries that require wastewater treatment and the best approaches for each.
1. Textile
Every day, textile manufacturing plants use many dyes and chemicals that create harmful wastewater, posing risks to human health and the environment. They typically use these wastewater treatment processes to remove pollutants from water:
- Absorption: Absorption binds liquid wastewater molecules to a solid, like active carbon.
- Activated sludge: This process combines aeration and additional bacteria to break down organic substances in the wastewater. The plant recycles the sludge at the end of the process.
- Aeration: Aeration adds oxygen to a wastewater column, allowing beneficial bacteria to break down organic components.
- Coagulation-flocculation: The plant introduces polymers to wastewater, combining small contaminant particles into bigger clusters.
- Moving bed bioreactor (MBBR): During moving bed bioreactor, water enters an aeration tank with media made of small plastic chips. The media produce biofilm organisms, which remove waste from the water.
2. Food and Beverage
Treating wastewater from food and beverage processing plants — such as dairy, poultry, produce and grain — can be a challenge. The water’s chemical composition varies significantly depending on the production line. Food processing plants have stringent environmental regulations to meet. Additionally, food industry wastewater has high biochemical oxygen demand (BOD).
Food and beverage facilities often use lagoon aeration to treat wastewater. Sufficient aeration gives bacteria enough oxygen to break down waste and comply with discharge guidelines. The right equipment, a properly maintained aeration system and adequate mixing and oxygen help prevent issues like sludge buildup during treatment.
Membranes with built-in check valves and PFTE-coated membranes help increase airflow to manage fluctuation, making it easier to handle high organic and inorganic compounds in wastewater.
3. Chemical
In the chemical industry, organic compounds can quickly build up in water, making proper wastewater treatment critical. Process water, effluents and stormwater can carry BOD and chemical oxygen demand (COD) compounds, causing an organic imbalance.
Chemical wastewater treatment involves removing larger waste solids, then shifting to smaller compounds. Aeration systems and diffusers help chemical manufacturing plants remove harmful substances from wastewater faster and more frequently.
Aeration systems — like MBBR and retrievable systems — add oxygen to the water. Diffusers create bubbles and push air into the water. The bubbles interact with the bacteria in the water tank, breaking down waste to enhance water quality.
4. Wine, Spirits and Beer
Producing wine, beer and spirits requires large amounts of water each day. Many by-products and contaminants result from the production process, including grape seeds, stems, stalks, skins, starch, grains, sugar and sludge. Wastewater from this industry can also contain chemicals from cleaning agents and other organic compounds.
Finding the right wastewater treatment system for wine, beer and spirits production is essential. Though this depends on numerous factors unique to the plant, some common processes include:
- MBBR: Using an aeration tank with water, MBBR uses biofilm growth to remove organic matter from wastewater.
- Integrated fixed film activated sludge (IFAS): IFAS wastewater treatment systems mix biofilm with an activated sludge basin or combine water with activated sludge.
- Tertiary treatment: Tertiary wastewater treatment helps make water clean enough to drink or reuse in industrial water processes.
Choose SSI for All Your Wastewater Needs
Whether you work in textile manufacturing, food and beverage processing, mining and quarry or another water-using industry, SSI Aeration, Inc. is your source for superior wastewater treatment solutions. As a global leader in water treatment equipment design and manufacturing, you can trust SSI to help you find solutions suited to your facility’s unique requirements.
Offering a variety of diffusers and membranes for wastewater aeration, you can find everything you need here. If you’re ready to improve your wastewater treatment processes with high-quality equipment, contact SSI Aeration, Inc. today to find the right wastewater treatment products for your plant.
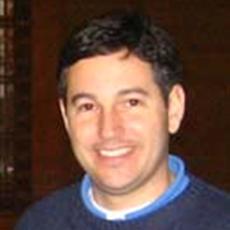
Mr. Frankel co-founded SSI in 1995 with experience in design and distribution of engineered systems. He is in charge of sales, marketing and operations in the company. Mr. Frankel holds multiple US patents related to diffusers. He is a graduate of Washington University in St. Louis.